An automatic baby diaper machine is a complex piece of machinery that streamlines the process of producing disposable baby diapers.
Raw material preparation
Key materials include non-woven fabric, absorbent polymer, fluff pulp, elastic materials, adhesive, and a moisture-proof backsheet. These materials are loaded onto the machine as large rolls.
Forming the absorbent core
The fluff pulp is defibrated and mixed with the superabsorbent polymer (SAP). This mixture forms the absorbent core, which is responsible for retaining fluids.
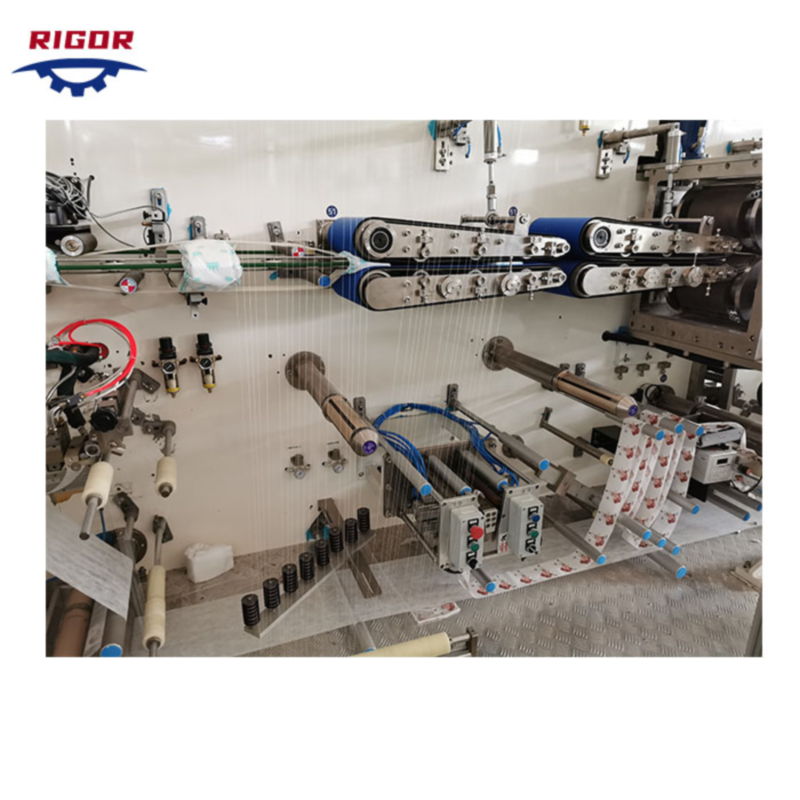
Formation of the non-woven top and bottom layers
The non-woven fabric is unrolled onto the conveyor belt, creating both the top layer (in contact with the baby’s skin) and bottom layer (moisture-proof backsheet) of the diaper.
Applying the absorbent core
The absorbent core is placed between the top and bottom layers and bonded using adhesive or thermal bonding.
Adding elastic materials
Elastic materials are added around the leg cuffs and waistband to ensure a snug fit and prevent leakage. These materials are stretched and adhered to the non-woven layers.
Cutting and shaping
The continuous diaper material is cut and shaped into individual diapers using rotary or ultrasonic cutting techniques. This process also forms the front and back parts of the diaper.
Adding fastening tapes or hook-and-loop closures
Adhesive fastening tapes or hook-and-loop closures are added to the front and back parts of the diaper to secure it around the baby’s waist.
Folding and packaging
The individual diapers are folded, stacked, and packaged into bags or boxes, ready for distribution.
Throughout the entire process, quality control measures are implemented to ensure that the diapers meet safety and performance standards. Modern diaper machines can produce hundreds or even thousands of diapers per minute, making them highly efficient and cost-effective for manufacturers.